Hey there, forging enthusiasts! If you're diving into the world of metalworking or simply curious about how some of the strongest and most reliable components are made, you're in the right place. Precision forged components are everywhere, from the cars we drive to the airplanes that take us across the globe. They're the unsung heroes of modern engineering. But what exactly does precision forged mean, and why is it so important? Let’s dig in and find out, shall we?
When it comes to manufacturing, precision is everything. Whether you're talking about aerospace parts, automotive components, or industrial machinery, getting the details right can make or break the final product. Precision forged technology has revolutionized the way we create durable, high-performance parts. It’s not just about making things stronger—it’s about doing it smarter.
So, whether you're an engineer, a hobbyist, or someone who's just fascinated by the science of metalworking, this article is here to give you the lowdown on precision forged components. We’ll cover everything from the basics to advanced techniques, so buckle up and get ready to learn something new!
Read also:Unboxing Dreams A Tiktokers Exciting Headboard Journey
Here's a quick glance at what we'll be exploring:
- What is Precision Forging?
- Types of Forging Processes
- Benefits of Precision Forged Components
- Applications of Precision Forged Parts
- Materials Used in Precision Forging
- The Precision Forging Process
- Quality Control in Precision Forging
- Cost Considerations for Precision Forging
- The Future of Precision Forging
- Wrapping It Up
What is Precision Forging?
Alright, let’s start with the basics. Precision forging is a manufacturing process where metal is shaped under high pressure and temperature to produce components with exceptional strength and durability. Unlike traditional forging methods, precision forging focuses on minimizing material waste and achieving tighter tolerances. This means the final product is not only stronger but also more consistent in shape and size.
Now, here’s the kicker: precision forging isn’t just about brute force. It’s a delicate balance of science and art. The process involves heating the metal to its optimal forging temperature and then using powerful presses or hammers to shape it into the desired form. The result? Components that can withstand extreme conditions while maintaining their integrity.
Why Precision Forging Matters
Think about it like this: every time you step into a car, you’re trusting hundreds of precision forged parts to keep you safe. The engine block, transmission gears, and suspension components—all of these rely on precision forging to ensure they perform flawlessly. Without this technology, modern transportation as we know it simply wouldn’t exist.
Types of Forging Processes
Not all forging is created equal. Depending on the application and material, different forging techniques are used to achieve the desired results. Let’s take a look at some of the most common methods:
- Open Die Forging: This is one of the oldest forging techniques, where the metal is placed between two dies and shaped manually. It’s great for large components but lacks the precision of other methods.
- Closed Die Forging: Also known as impression die forging, this process uses pre-shaped dies to form the metal. It’s ideal for producing complex shapes with high accuracy.
- Press Forging: In this method, the metal is deformed slowly under continuous pressure. It’s perfect for creating large, heavy components.
- Roll Forging: This technique involves rolling the metal between two rotating rolls to achieve the desired shape. It’s commonly used for producing long, cylindrical parts.
Which Method is Best for Precision Forging?
When it comes to precision forged parts, closed die forging and press forging tend to dominate. These methods offer the control and accuracy needed to produce components with tight tolerances. But as with anything in engineering, the choice depends on the specific requirements of the project.
Read also:Lesego Marakalla Shares Rare Glimpse Of Her Personal Life
Benefits of Precision Forged Components
So, why should you care about precision forged parts? Well, there are plenty of reasons. Let’s break them down:
- Increased Strength: Precision forging aligns the grain structure of the metal, resulting in components that are significantly stronger than their cast or machined counterparts.
- Improved Durability: The process eliminates internal defects and porosity, leading to parts that can withstand harsh environments and heavy loads.
- Reduced Material Waste: By optimizing the forging process, manufacturers can minimize waste and reduce costs.
- Consistent Quality: Precision forging ensures that each component meets strict specifications, reducing the need for post-processing.
How Precision Forging Impacts Performance
Imagine this: you’re designing a high-performance engine for a race car. Every gram of weight and every micron of tolerance matters. Precision forged components allow you to push the limits of performance without compromising safety. It’s like giving your design a superpower.
Applications of Precision Forged Parts
Precision forged components are everywhere, and their versatility makes them indispensable in various industries. Here are just a few examples:
- Aerospace: Jet engines, landing gear, and structural components all rely on precision forging to ensure reliability at 30,000 feet.
- Automotive: From engine blocks to suspension systems, precision forged parts are the backbone of modern vehicles.
- Oil and Gas: Pipelines, valves, and drilling equipment need to withstand extreme pressures and temperatures, making precision forging a natural fit.
- Medical Devices: Surgical instruments and implants require the utmost precision and durability, which precision forging delivers.
Real-World Examples of Precision Forging
Take a look at the Boeing 787 Dreamliner. Its landing gear is made from precision forged titanium, ensuring it can handle the stresses of takeoff and landing. Or consider Formula 1 cars, where every component is engineered to perfection using precision forging techniques. These examples highlight the critical role precision forged parts play in modern technology.
Materials Used in Precision Forging
Not all metals are suitable for precision forging. The choice of material depends on factors like strength, ductility, and cost. Some of the most commonly used materials include:
- Steel: Known for its excellent strength-to-weight ratio, steel is the go-to material for many precision forged parts.
- Titanium: Lightweight yet incredibly strong, titanium is ideal for aerospace and medical applications.
- Aluminum: Perfect for reducing weight without sacrificing strength, aluminum is widely used in automotive and aerospace industries.
- Super Alloys: These high-performance alloys are designed to withstand extreme temperatures and pressures, making them perfect for jet engines.
Selecting the Right Material
Choosing the right material is crucial for achieving the desired performance. Factors like operating conditions, cost constraints, and manufacturing requirements all play a role in the decision-making process. It’s not just about picking the strongest material—it’s about finding the one that fits the job best.
The Precision Forging Process
Now that we’ve covered the basics, let’s dive into the nitty-gritty of the precision forging process. Here’s a step-by-step breakdown:
- Material Preparation: The metal is cut to size and cleaned to remove any impurities.
- Heating: The metal is heated to its optimal forging temperature, which varies depending on the material.
- Forging: The heated metal is placed in the forging dies and shaped under high pressure.
- Cooling and Heat Treatment: After forging, the part is cooled and often undergoes heat treatment to enhance its properties.
- Finishing: Any final machining or surface treatments are applied to achieve the desired finish.
Key Considerations in Precision Forging
Temperature control, die design, and material selection are all critical factors in the precision forging process. Getting these details right ensures that the final product meets the required specifications and performs as expected.
Quality Control in Precision Forging
Quality control is the backbone of precision forging. Without it, even the best processes can produce subpar results. Manufacturers use a variety of techniques to ensure that each component meets the highest standards:
- Inspection: Components are inspected using advanced imaging and measurement tools to verify dimensions and surface quality.
- Testing: Mechanical and chemical tests are performed to ensure the material properties meet the required specifications.
- Documentation: Every step of the process is documented to ensure traceability and compliance with industry standards.
The Importance of Quality Control
In industries like aerospace and medical devices, failure is not an option. Quality control ensures that every precision forged part is reliable and safe to use. It’s the difference between a component that lasts for years and one that fails prematurely.
Cost Considerations for Precision Forging
While precision forging offers many benefits, it’s not without its costs. Factors like material selection, tooling, and production volume all impact the overall price. However, the long-term savings from reduced waste and improved performance often outweigh the initial investment.
When Does Precision Forging Make Sense?
If you’re producing high-volume, high-performance parts, precision forging is often the most cost-effective solution. It’s also a great choice for critical components where failure is not an option. But for low-volume or prototype runs, other manufacturing methods might be more economical.
The Future of Precision Forging
As technology continues to evolve, so does the field of precision forging. Advances in materials science, automation, and AI are opening up new possibilities for manufacturers. Here are a few trends to watch:
- Advanced Materials: New alloys and composites are being developed to push the boundaries of performance and durability.
- Smart Manufacturing: Automation and AI are being used to optimize the forging process, reducing costs and improving quality.
- Sustainability: Manufacturers are increasingly focusing on reducing waste and energy consumption in their operations.
What’s Next for Precision Forging?
The future looks bright for precision forging. As industries continue to demand stronger, lighter, and more efficient components, the technology will only become more sophisticated. It’s an exciting time to be involved in this field!
Wrapping It Up
There you have it, folks—a comprehensive guide to precision forged components. From the basics to the future trends, we’ve covered everything you need to know about this fascinating technology. Precision forging isn’t just about making parts—it’s about creating solutions that drive innovation and push the boundaries of what’s possible.
So, whether you’re an engineer designing the next generation of aircraft or a hobbyist building your dream car, precision forging has something to offer. Take a moment to reflect on the information we’ve shared and consider how it can benefit your projects. And don’t forget to share this article with your friends and colleagues!
Got any questions or thoughts? Drop a comment below, and let’s keep the conversation going. Until next time, stay curious and keep forging ahead!

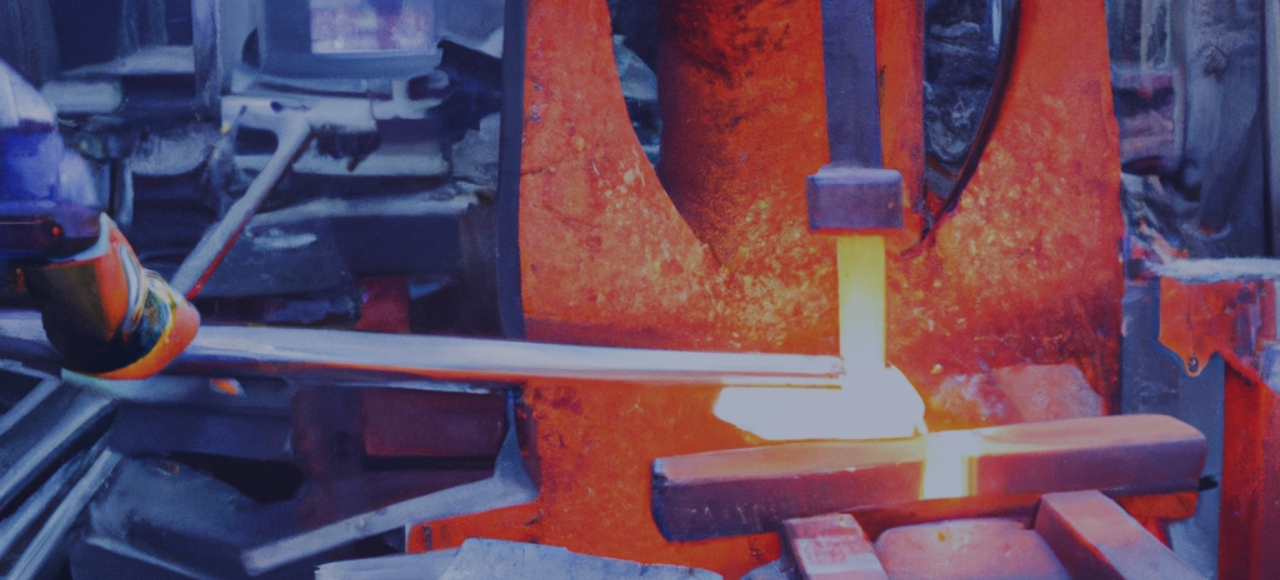
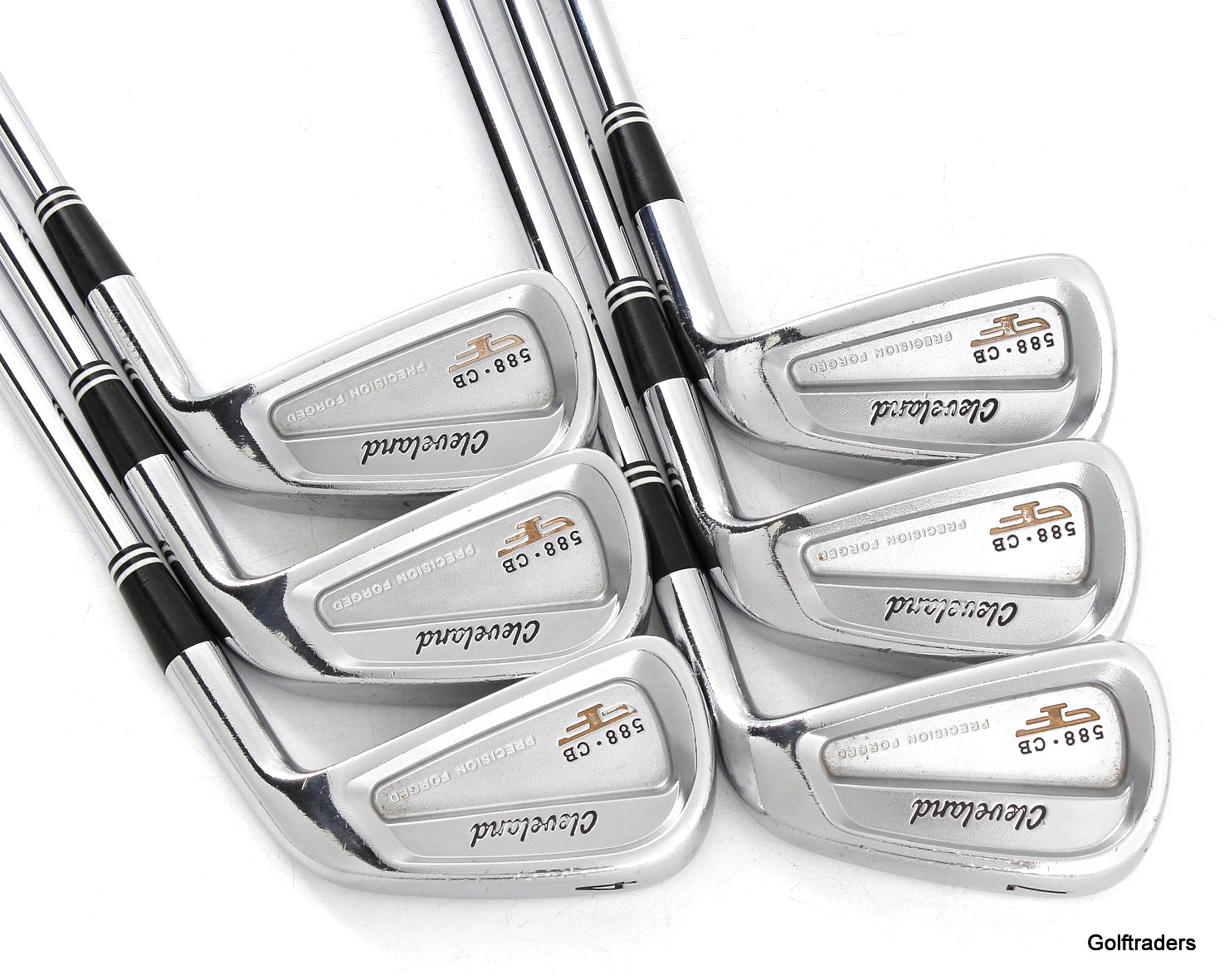